Maximizing Equipment Efficiency Through Packaging Machine Repair
Maximizing Equipment Efficiency Through Packaging Machine Repair
Blog Article
Quick and Reliable Product Packaging Equipment Repair Service Provider to Decrease Downtime
In the competitive landscape of production, the performance of product packaging operations hinges on the integrity of machinery. Quick and trusted repair work services are crucial in alleviating downtime, which can lead to considerable economic losses and operational setbacks.
Relevance of Timely Repair Works
Prompt repair work of packaging makers are crucial for keeping operational effectiveness and minimizing downtime. In the busy setting of manufacturing and packaging, also minor malfunctions can lead to substantial hold-ups and productivity losses. Addressing concerns without delay ensures that makers run at their optimum capability, thus securing the flow of procedures.
Furthermore, timely and normal upkeep can avoid the acceleration of minor issues into major failures, which typically incur higher repair service expenses and longer downtimes. An aggressive technique to equipment repair work not only preserves the stability of the tools yet additionally boosts the overall reliability of the production line.
Additionally, prompt fixings add to the longevity of packaging equipment. Equipments that are serviced promptly are less likely to experience excessive wear and tear, allowing organizations to maximize their investments. This is especially vital in markets where high-speed packaging is crucial, as the demand for regular performance is vital.
Benefits of Reliable Solution Service Providers
Dependable company play a crucial role in guaranteeing the smooth procedure of packaging devices. Their competence not just boosts the performance of repairs however likewise contributes considerably to the long life of tools. Reputable service carriers are geared up with the technological knowledge and experience essential to diagnose issues properly and execute efficient solutions rapidly. This lowers the risk of persisting troubles and makes certain that makers run at ideal efficiency levels.
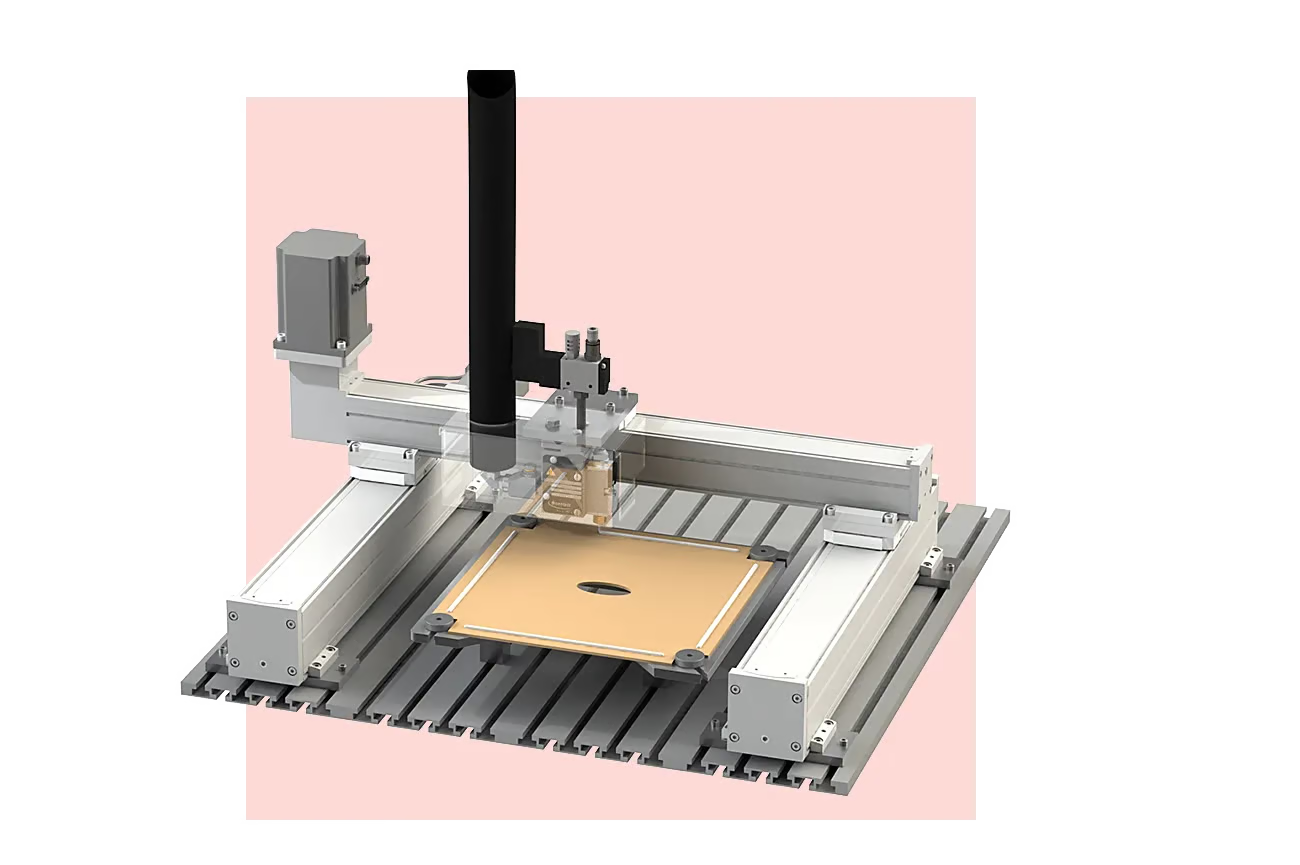
In addition, a respectable company offers detailed support, consisting of training and assistance for personnel on maker operation and upkeep finest methods. This not just equips workers however also grows a culture of safety and security and efficiency within the organization. On the whole, the benefits of engaging trustworthy provider expand past prompt repair work, positively affecting the whole functional process of packaging processes.
Typical Packaging Equipment Issues
In the realm of product packaging procedures, various issues can compromise the effectiveness and performance of makers. One prevalent problem is mechanical failing, frequently stemming from deterioration or inadequate maintenance. Parts such as electric motors, belts, and equipments might stop working, resulting in failures that halt production. Another usual problem is misalignment, which can cause jams and irregular product packaging, influencing item high quality and throughput.
Electric problems can additionally disrupt product packaging operations. Defective circuitry or malfunctioning sensing units may result in irregular equipment actions, creating hold-ups and enhanced operational expenses. Additionally, software problems can impede the equipment's programs, causing functional ineffectiveness.
Irregular product flow is another critical issue. This can emerge from variants in item size, shape, or weight, which might impact the maker's capability to manage things properly. Not enough training of drivers can intensify these problems, as inexperienced personnel might not recognize very early indicators of malfunction or might misuse the devices.
Attending to these typical packaging maker concerns quickly is important to keeping performance and guaranteeing a smooth procedure. Routine inspections and proactive upkeep can substantially reduce these problems, promoting a dependable packaging atmosphere.
Tips for Reducing Downtime
To reduce downtime original site in product packaging procedures, carrying out an aggressive maintenance technique is crucial. Frequently arranged upkeep checks can determine prospective issues prior to they escalate, guaranteeing equipments operate effectively. Developing a routine that consists of lubrication, calibration, and inspection of critical elements can substantially reduce the regularity of unforeseen breakdowns.
Educating staff to operate machinery correctly and acknowledge very early caution indicators of breakdown can additionally play a crucial duty. Encouraging operators with the understanding to do standard troubleshooting can avoid minor problems from creating major hold-ups. Maintaining a well-organized stock of essential spare parts can accelerate repair services, Visit This Link as waiting for parts can lead to prolonged downtime.
Additionally, recording device performance and upkeep tasks can help identify patterns and frequent issues, permitting targeted interventions. Integrating sophisticated monitoring innovations can give real-time data, enabling anticipating upkeep and minimizing the risk of abrupt failures.
Lastly, cultivating open interaction between drivers and maintenance teams makes certain that any abnormalities are quickly reported and attended to. By taking these aggressive steps, businesses can improve functional effectiveness and significantly decrease downtime in packaging processes.
Choosing the Right Repair Service
Choosing the suitable repair work service for product packaging machines is a critical choice that can considerably impact functional effectiveness. Begin by evaluating the service provider's experience with your particular kind of product packaging devices.
Next, think about the provider's credibility. Seeking responses from other companies within your industry can give understandings right into reliability and top quality. Certifications and partnerships with identified devices manufacturers can additionally suggest a commitment to excellence.
Additionally, examine their reaction time and accessibility. A provider who can use punctual assistance reduces downtime and keeps manufacturing flow constant. It's likewise critical to ask concerning warranty and service guarantees, which can mirror the self-confidence the copyright has in their work.
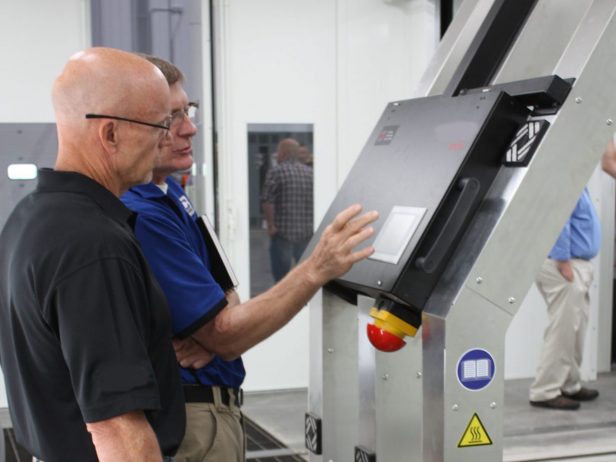
Final Thought
In final thought, the relevance of trusted and fast product packaging device repair service solutions can not be overstated, as they play an important role in decreasing downtime and guaranteeing functional effectiveness. By focusing on timely repairs and selecting reliable company, click for info businesses can successfully keep and resolve typical problems performance. Applying proactive maintenance practices and purchasing team training further boosts the long life of product packaging machinery. Eventually, a strategic strategy to repair solutions fosters a more durable manufacturing environment.
Timely fixings of packaging machines are important for keeping operational effectiveness and decreasing downtime.Furthermore, prompt repair services add to the durability of packaging equipment. Overall, the benefits of engaging trustworthy service carriers extend beyond prompt repairs, positively impacting the whole functional workflow of product packaging processes.
Report this page